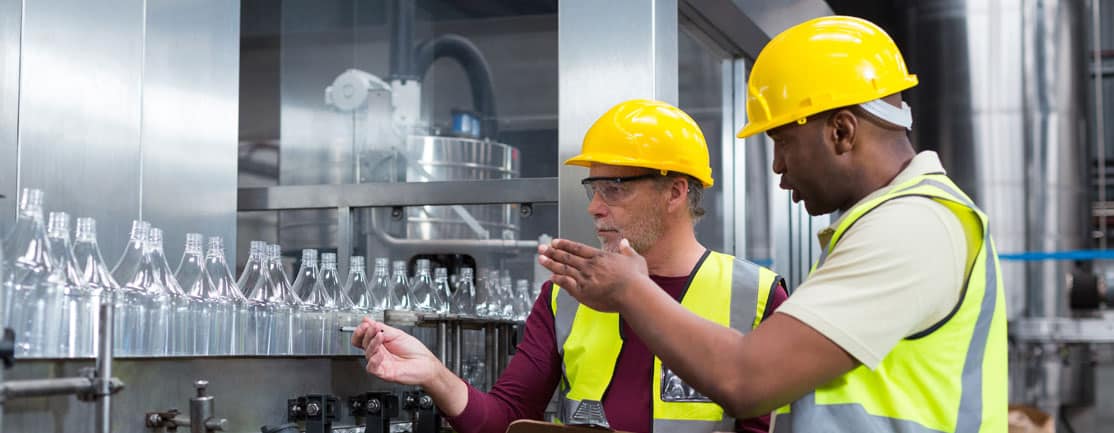
Today’s manufacturers are navigating tough and uncertain times. Our digitized and interconnected global economy creates enormous opportunities, encourages challenging competitors, eliminates weaker players and demands future sustainability – all of which has been overwhelmingly exacerbated by the COVID-19 pandemic. As many industry leaders can attest to, the balance between supply and demand can tilt in the blink of an eye. Thus, the pressure is on to improve production efficiencies, customer responsiveness and market agility to maintain a competitive advantage. An opportunity lies in developing a rapid deployment strategy that addresses one of most manufacturers’ biggest vulnerabilities: waste.
What is rapid deployment?
The rapid deployment process is a focused, time-bound response to key areas of losses and wastes within a business. The emphasis is on speed; using up-to-date information and relevant tools to identify and resolve excessive issues of loss and waste. No two businesses will experience the exact same issues, which is why the first step in the rapid deployment process is a “loss and waste” analysis.
In this video , TRACC specialist David Rogers uses an example to outline the rapid deployment process and loss and waste analysis. Here is an excerpt from his interview:
“Let us use overall equipment effectiveness (OEE) as an example. If we situate our example in a packaging line, the loss and waste analysis will indicate the reasons for underperformance against the theoretical target pegged to that line. The organization in question can then set its OEE starting point based on accurate analysis. For the sake of this example, let’s make that starting point 45%. Business leaders can then focus on integrating Lean principles in their operations to deliver continuous improvement (CI) gains over, say, a three-month period. The aim of rapid deployment is not to crack the whip to hit 100% OEE in as short a timeframe as possible. Rather, its job is to decide which tools will have the fastest impact on improving the packaging line’s performance and put a governance process and a structure in place that will allow such gains to happen as quickly as possible.”
How to approach a loss and waste analysis for the best rapid deployment results
The loss and waste analysis is the crucial first step in the rapid deployment process. Why? Because given the need for speed in today’s turbulent times, the loss and waste analysis enables business leaders to identify and select some quick-win projects that will show fast gains. However, the analysis itself requires a careful and methodical approach – otherwise, major operational pain points can easily be overlooked and valuable insights lost.
Manufacturers leading their organization’s rapid deployment processes must pay attention to the following steps to address all operational pain points successfully:
1. Understand the different types of waste. |
2. Confirm the organization’s improvement strategy and its key objectives. |
3. Consider the organization’s main loss categories. |
4. Use efficient mechanisms to measure the losses and, if possible, quantify them in financial terms. |
5. Analyze losses in detail and prioritize major loss areas. |
6. Summarize the findings in a standardized template. |
7. Identify those losses that have the potential to be quick-win improvement projects. |
8. Make recommendations to the senior leadership team. |
9. Decide and agree upon a review period. |
10 Begin the rapid deployment process. |
The seven deadly wastes
Fifty years ago, Taiichi Ohno, the chief engineer at Toyota at the time, developed the concept of the seven deadly wastes. Today, Lean manufacturing practitioners still refer to the seven deadly waste areas: overproduction, motion, waiting, inventory, correction, processing and transportation. These various components of production are prime sites of inefficient practices and processes that stagnate company growth. That said, they respond well to rapid deployment processes and, when run according to CI principles, can turn a company’s fortunes around fast.
The table below provides manufacturers with a simple breakdown of the seven deadly wastes, what they entail and how to spot them.
The 7 Deadly Wastes | Description | What to look for |
1. Overproduction | Producing more than what the customer requires. | High levels of work in process (WIP), unclear production plans and poor schedule adherence. |
2. Motion | Any movement of equipment or an employee that does not add value. | Excessive movement of operators and equipment, location of equipment and materials is not clear, controls and displays are not easily accessible, operators are often in uncomfortable positions. |
3. Waiting | Any employee or equipment that is available but waiting for some form of input. | Operators waiting at idle equipment, poorly defined or no standard operating procedures, operators or maintenance employees are not working or are searching for items. |
4. Inventory | Excessive raw material, WIP or finished goods. | Inventory level limits are exceeded or are not set, material is in poor condition, existence of obsolete inventory. |
5. Correction | Defective product requiring rework. | Presence of large waste bins, large holding areas, rework areas and over-inspection. |
6. Processing | Using excessive capacity or energy without adding value. | Furnaces or ovens not running, equipment not operating at optimum speed, high-capacity equipment being used for small tasks. |
7. Transportation | Unnecessary movement and handling of material. | Long distances between processing workstations, many conveyors or parts crossing lines, poor flow and materials handled multiple times. |
Benefits of the rapid deployment process – and how to guarantee them
In short, a relevant, well-led and well-orchestrated rapid deployment process can turn inefficient production sites into lean, well-oiled operating areas – fast. These quick wins deliver financial gains, improve employee performance, encourage cross-functional collaboration, and build resources, confidence and enthusiasm for ongoing improvements across the business.
However, manufacturers embarking on a rapid deployment process must address the following six points to ensure they reap the benefits in the defined timeline.
1. Determine the scope
A crucial element in implementing a successful rapid deployment strategy is determining its scope before hitting play. Those in charge of implementation must clarify the following in their strategic design:
- How will teams execute rapid deployment in quick-win improvement areas? Will they begin with a single pilot project in a pilot area? Or, will they run rapid deployment processes across an entire site in multiple major loss areas guided by the same improvement focus?
- What “pain points” will the rapid deployment process focus on? This ultimately comes down to the loss and waste analysis which confirms the business area’s main improvement objective. For example, does the site want to improve OEE in a packaging line, reduce downtime, improve the quality of output or increase production output and/or speed?
2. Put a governance structure in place
To achieve the organization’s desired gains and clearly defined targets, the identified areas for improvement need project owners who can govern the rapid deployment process, self-assess and work together on an agreed upon implementation strategy – also known as a flight plan.
3. Choose the tools and methodologies
The project owners will need defined tools and methodologies to achieve the targets set in their areas marked for improvement. A useful project management tool is an A3 report which will help them agree upon a flight plan. As well as being a one-page problem-solving report that identifies the root cause of a problem and outlines steps to address it, an A3 also acts as an effective, transparent project management tool.
Download our How-to guide: How to use a problem-solving A3 report to find out more about this useful tool.
The project owners also need to choose the methodology best suited to developing their flight plans. Their methodology of choice could be DMAIC (Define, Measure, Analyze, Improve and Control), short interval control or setup time reduction.
“Any of these methodologies can be used,” says David, “as they will all contribute to developing a relevant and actionable flight plan that will, if we refer back to our OEE example, improve performance in the packaging line from 45% to 70% by week 12.”
4. Track the improvement project
Once leadership has allocated project owners and agreed upon flight plans and methodologies, David Rogers talks about the importance of having “a very structured weekly governance forum to drive positive accountability and provide support”.
Clear communication is vital throughout the rapid deployment process to keep everyone involved on track. A one-hour weekly check-in gives project owners a platform to assess whether they are going to achieve their A3 goals, share solutions, give updates on their specific projects, and provide actions for the leadership team to help them reach their improvement targets.
5. Communicate through visual management
Using visual management to communicate information about improvement projects undergoing rapid deployment works incredibly well. Not only does it keep everyone involved and up to date in an efficient manner, it provides teams with transparent feedback for immediate action. These visual updates can follow a project’s timeline from start to finish – and they are easily shared on company websites as well as on electronic or manual noticeboards set up in strategic workplace locations.
Visual management makes information accessible in compelling, concise and shareable formats such as:
- Graphs, charts, infographics that show, for example, set targets against actual achievements
- Photographs of site areas before and after improvement
- Work stream team information
- Breakthrough or quick-win project information
- Completed A3 reports
6. Develop problem-solving and coaching capability
Achieving improvement is essentially solving a problem. Thus, the project owners need basic problem-solving skills as well as some analytical and facilitation capabilities to carry out their roles successfully. Leadership needs to review their project owners’ existing skills sets and provide the requisite training and upskilling to increase existing levels of competence.
Once the project owners are up and running confidently, coaching and facilitation training needs to be made available to middle managers, team leaders and eventually team members themselves. This will have an enormous impact on the organization’s ability to achieve quick results. By the end of the rapid deployment process, coaching and problem-solving need to be built into the organization’s cultural core.
Successful rapid deployment depends on leadership
The role of leadership throughout the rapid deployment process, from loss and waste analysis to achieving improvement targets, is critical. The success of any improvement project is directly related to the level of leadership buy-in, support and energy. Leaders need to use their words and actions to set an example that encourages accountability and boosts morale. There is no room for backseat leaders when it comes to improving production-related inefficiencies. Rapid deployment requires responsive, decisive and involved leaders who are not afraid to assess and, if necessary, change their leadership styles and behaviors for more positive results.
On a practical level, leaders can help ensure an inclusive rapid deployment process by initiating a daily management system (DMS) at site level to provide project owners and teams with a structured set of standard procedures to self-assess and continuously improve their performance. Initiating a daily operations review (DOR) meeting can also help teams achieve their targets by managing improvement and addressing any issues as they happen.
As more manufacturers realize the importance of rapid deployment processes to improve their business operations and market reputation, particularly as customers become more demanding, company leaders need to step up and lead the change. In fact, as Rogers puts it: “Another way of describing rapid deployment is simply: competent, positive and moral leadership.”
Interested in developing a customized rapid deployment strategy for your business? Contact us to find out more.